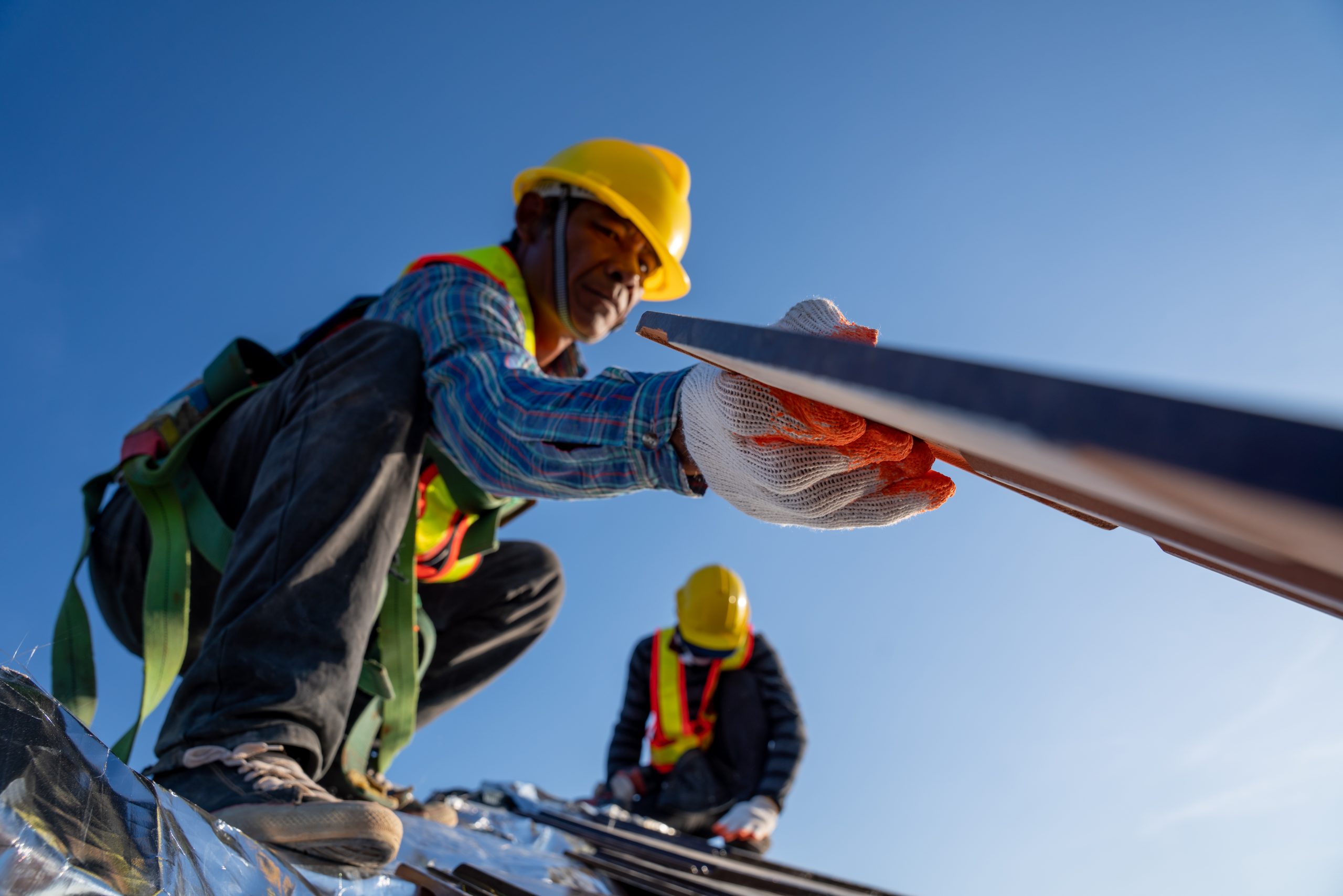
A Comparison of Commercial Roofing Systems—Process, Longevity, Pros and Cons
Lots of options. Lots of variables to sort through. Lots of advantages and disadvantages. Lots of decisions are to be made.
When it comes to figuring out what type of roofing system is best for your commercial property, you’ve got plenty of things to work out. Attaining your best results involves having a detailed understanding of your people and business. Also knowing your physical location and type of facility. As well as analyzing the roofing systems available to you. This includes upfront costs and long-term warranties. When it comes to actually doing the job, the use of top-quality materials and installation by qualified professionals is a must. So is performing both routine maintenance and taking care of immediate emergency repairs over the long haul.
To help with all that, check the chart for an overview of six common commercial roofing choices. We’ve also included a brief description of the processes and estimated longevity. There is also a listing of pros and cons associated with each one.
Pros and Cons of Commercial Roofing Systems
TYPE OF ROOF | PROCESS | PROS | CONS | LIFESPAN |
Built-up Systems | ||||
BUR ‒ Built-up roofing |
Commonly called tar-and-gravel, roofs are built of multiple, alternating layers of bitumen (asphalt) and reinforcing fabrics. They’re topped with a protective layer of gravel or stone. In use 100+ years, BUR offers well-proved effectiveness. |
|
|
15-30 yrs. |
TYPE OF ROOF | PROCESS | PROS | CONS | LIFESPAN |
Built-up Systems (continued) | ||||
Mod bit – Modified bitumen roofing |
Similar to BUR, mod bit has fewer layers, more adhesive options. Plys (layers) are sealed down to the roof deck or coverboard with no seams. Three different surfaces are available, mineral, foil, or laminate, with ceramic coating. |
|
|
10-20 yrs. |
TYPE OF ROOF | PROCESS | PROS | CONS | LIFESPAN |
Single-ply Membrane Systems | ||||
EPDM ‒ Ethylene propylene diene monomer |
AKA rubber roofing. EPDM is a thermoset process using a membrane manufactured offsite with all ingredients incorporated into rolls of material. Chemically cross-linked polymers become rigid once applied. One layer of membrane is applied to the roofing substrate. Seams are sealed between membranes with mechanical fasteners. |
|
|
15-25 yrs. |
TYPE OF ROOF | PROCESS | PROS | CONS | LIFESPAN |
Single-ply Membrane Systems (continued) | ||||
TPO – Thermoplastic roofing |
Also a rubber-like membrane system, thermoplastic roofing is made of synthetic substances that soften when heated, harden when cooled, and can be reshaped over time. Seams are heat-welded, melted together for a dependable bond. |
|
|
7-20 yrs.
|
PVC ‒ Polyvinyl chloride |
This is another type of thermoplastic system. Two layers of PVC material are reinforced with polyester plasticizers. Placed between plys to provide UV stability, flexibility, and prevent curling. Heat-welding keeps seams securely adhered together. |
|
|
15-30 yrs. |
TYPE OF ROOF | PROCESS | PROS | CONS | LIFESPAN |
Spray Foam Systems | ||||
SPF ‒ Spray polyurethane foam |
A specialized system, SPF blends two chemical elements together under heat and pressure. Forming a plastic that transforms from liquid to solid within seconds. Expanding 30 times in volume as it dries. Once hardened, a fully adhered roof surface results. The foam must be covered with an elastomeric coating of silicone, acrylic, urethane, or butyl rubber. Finished with a layer of crushed stone granules to prevent damage from UV radiation and other elements. Each roof is custom-created on-site and endlessly renewable with careful maintenance and regular elastomeric recoating. |
|
|
25-40+ yrs.
|
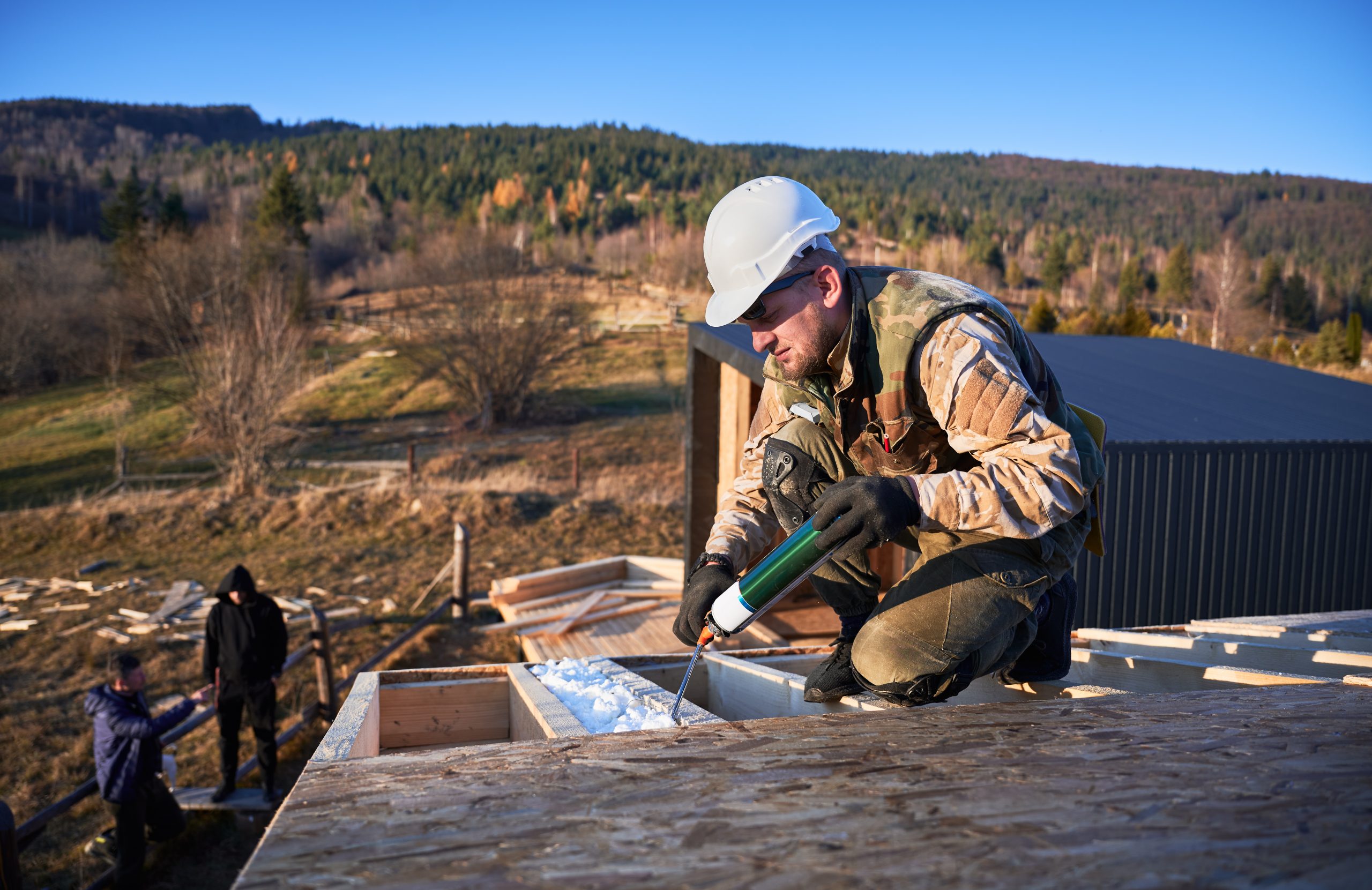
It should be noted that costs vary widely and are subject to volatility. At this writing (December 2022) per-square-foot pricing ranges from $2.00 at the low end to $10.50 or more at the top. Always work with a knowledgeable, qualified professional to get the roofing system that works best for you.