Commercial Low-Slope Roofing Basics – What You Need to Know
Commercial roofs are complicated. That’s because every instillation is essentially a custom application designed for a specific situation. Each solution must accommodate a complex combination of factors – the size of your building(s), age, purpose, location, climate, people, equipment, surroundings – which are constantly interacting to protect the structure and what’s happening inside. Find out which types of commercial roofing are right for you.
Since you’ll be living with your roofing decisions for a long time (15 to 40 or more years), you want to understand the options available to you, including what and how each type of commercial system works. Since the majority of commercial roofs are of the low-slope variety, this discussion focuses on those types of systems. And please don’t call them flat because they’re not. To work properly, a commercial roof must be slightly sloped. Typically, that means having a minimum pitch of one-fourth inch vertical to twelve-inch horizontal (¼:12 or 2 percent), but that can vary depending on the setting and roofing material. Roofs are considered low-slope up to 3:12 pitch.
Figuring out your ideal slope and the myriad other details associated with commercial roofing is why your best advice is to work with a qualified, experienced professional. He or she understands everything about roofing and can apply expertise developed through years of experience, industry training, and local knowledge to your situation.
What’s Under Your Roof Matters
It’s easy to think of your roof as what you can see. The reality is, multiple layers are involved in making your roof work.
- Structural decking is the bottom layer, forming the backbone of the entire system. Steel is the most common roof deck in U.S. commercial buildings, although this foundation must be carefully matched to each structure in order to give adequate support to all the materials and activities on top.
- A vapor control layer helps prevent water condensation from forming and reaching interior walls, ceilings, and attics, where it can cause structural elements to grow mold, rot, and collapse. Usually made of plastic or asphalt, a vapor barrier is especially important in northern climates where exterior temperatures are colder than those inside.
- Thermal insulation is a layer of material installed under the roof’s surface to create a barrier between inside and outside forces. It’s important to managing heating and cooling costs.
- Coverboard, while not always required, can improve the quality and extend the life of a roof. Made of gypsum or high-density polyiso foam, this thin, dense substrate goes directly below the surface, adding puncture resistance and protecting from hail, foot traffic, tools, and other intrusions that can damage the roof.
- The roofing membrane is the outer, top layer of a low-slope roof, sealing, waterproofing, and protecting the entire roofing assembly.
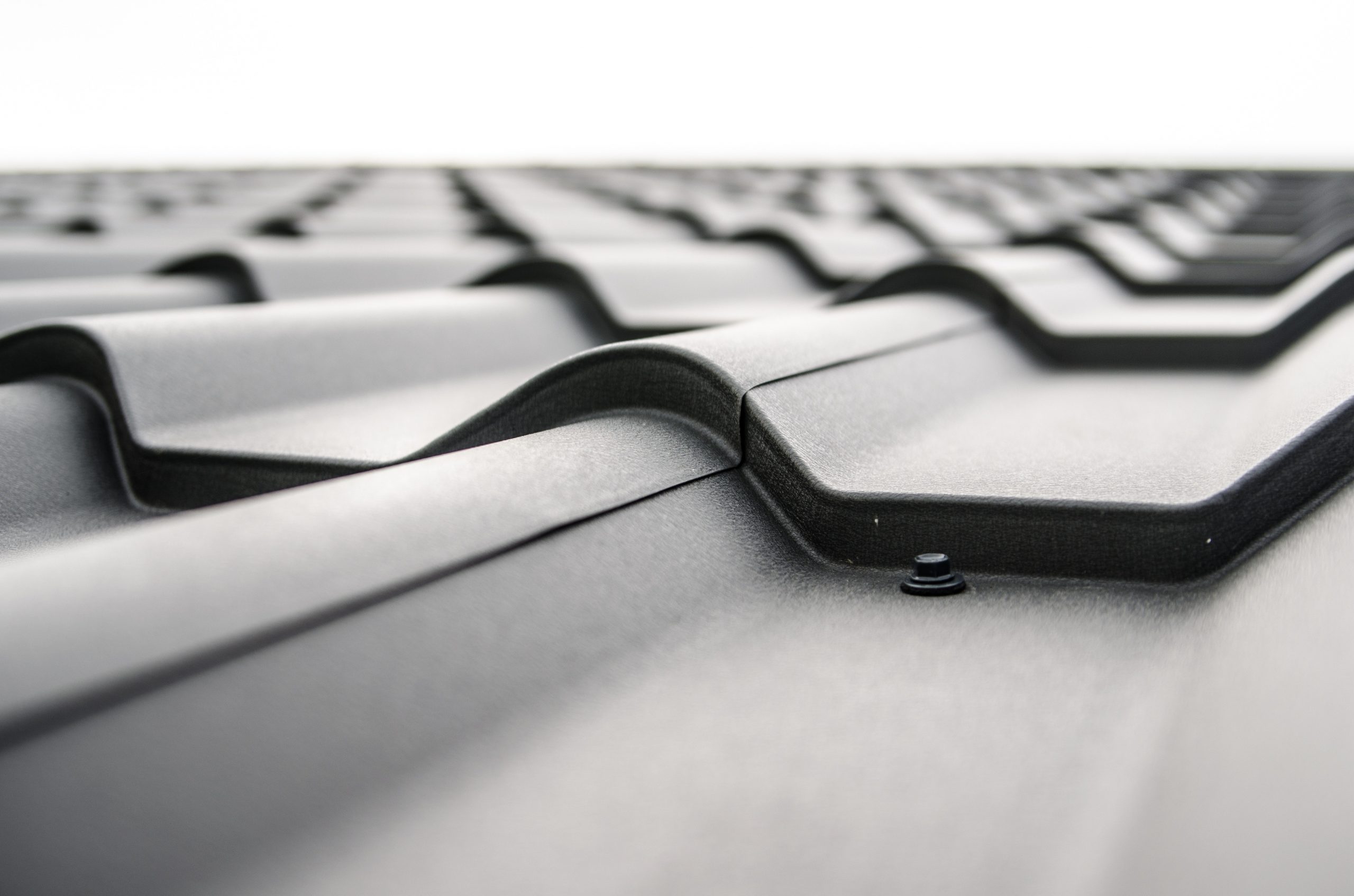
What’s Happening on the Surface Impacts Roofing Design
What goes on atop the membrane is an essential part of planning the correct roofing solution for you.
- Size and weight. The fact that commercial buildings are often large structures with huge roof surfaces is an important part of the design equation. Relatively lightweight roofing materials are essential in order for the building to support the weight.
- Water. Getting water, snow, hail, and anything else liquid off the roof quickly can be a challenge because low-slope systems may not easily drain. Standing water can cause leakage and also add dangerous weight, making an efficient drainage system essential.
- Foot traffic. Commercial roofs generally house HVAC equipment, solar panels, ventilation fans, skylights, cooling towers, and more on the surface. These add weight and require penetrations of the roof. Service and repair technicians will need to access these items from time to time, creating foot traffic and increasing the likelihood of punctures to the membrane. Making the surface durable enough to resist such damage adds much-needed longevity and functionality.
- Weather, UV rays, seasonal changes, wildlife. Weather, especially storms and sunlight, is one of the main things that can degrade a roof. Birds and other wildlife also cause damage. Every commercial roof must be designed to withstand the climate; reflective outer surfaces are particularly important to controlling the interior environment.
With all that going on, it’s easy to see why commercial roofing is such as challenge to design and maintain.
Three Types of Low-Slope Systems Are Commonly in Use
Single-ply roofing, built-up roofing, and modified bitumen roofing are the systems most commonly used in commercial, low-slope installations. Each has advantages and disadvantages, so you want to thoroughly investigate which application is appropriate for your situation. Your professional roofing consultant is a great asset in that regard.
- Single-ply roofing is a type of membrane that is manufactured offsite with all ingredients already incorporated into rolls of material. Launched in the 1965 when the first EPDM roof membrane was created (more about that below), single-ply systems consist of one layer (or ply) of membrane applied to the roofing substrate. Several types of single-ply roofing are in common use.
-
- Thermoset roofing incorporates polymers that are chemically cross-linked or vulcanized and is rigid once applied. EPDM (ethylene propylene diene monomer) is a type of synthetic rubber that for roofing purposes comes in varying thicknesses, in rolls up to 50 feet wide and 200 feet long. Lasting 15 to 20 years, EPDM roofs are durable, cost-effective, and fire- and weather-resistant. Downsides are seams between membranes that can fail and a utilitarian rubber look that’s effective but not particularly attractive.
- Thermoplastic roofing is made of synthetic substances that soften when heated, harden when cooled, and can be reshaped over time. It comes in two types: TPO (thermoplastic polyolefin) and PVC (polyvinyl chloride); the latter includes added plasticizers, the former does not, giving each unique properties suited to various situations. Both substances are impact and chemical-resistant, with a highly reflective white membrane that repels sunlight and helps energy efficiency. While upfront costs are higher than other options, long-term durability (20+ years) helps offset initial investment.
- Built-up roofing or BUR has been around for more than 100 years so is obviously very effective. This tar-and-gravel system consists of multiple, alternating layers of reinforcing fabrics adhered with asphalt and topped with a protective layer of gravel or stone. Because BUR is manufactured on the roof, this method is hot, messy, slow, and disruptive. It’s also heavy and leaks and tears are difficult to find and fix. Affordability is a big upside, along with as many built-up, redundant layers of protection as you want.
- Modified bitumen roofing is similar to BUR but with fewer layers and more adhesive options. Plies are sealed down to the roof with no seams, making the system strong, energy-efficient, and tear-resistant. But it’s not inexpensive, can be vulnerable to UV damage, and is prone to breakdowns if water is allowed to pond.
Like we said at the beginning: commercial roofs are complicated, as these brief descriptions make clear. And while each of these low-slope systems is effective, choices regarding which one to use must be site- and purpose-specific. The reward is knowing your facility is well protected and the valuable activity inside it secured.