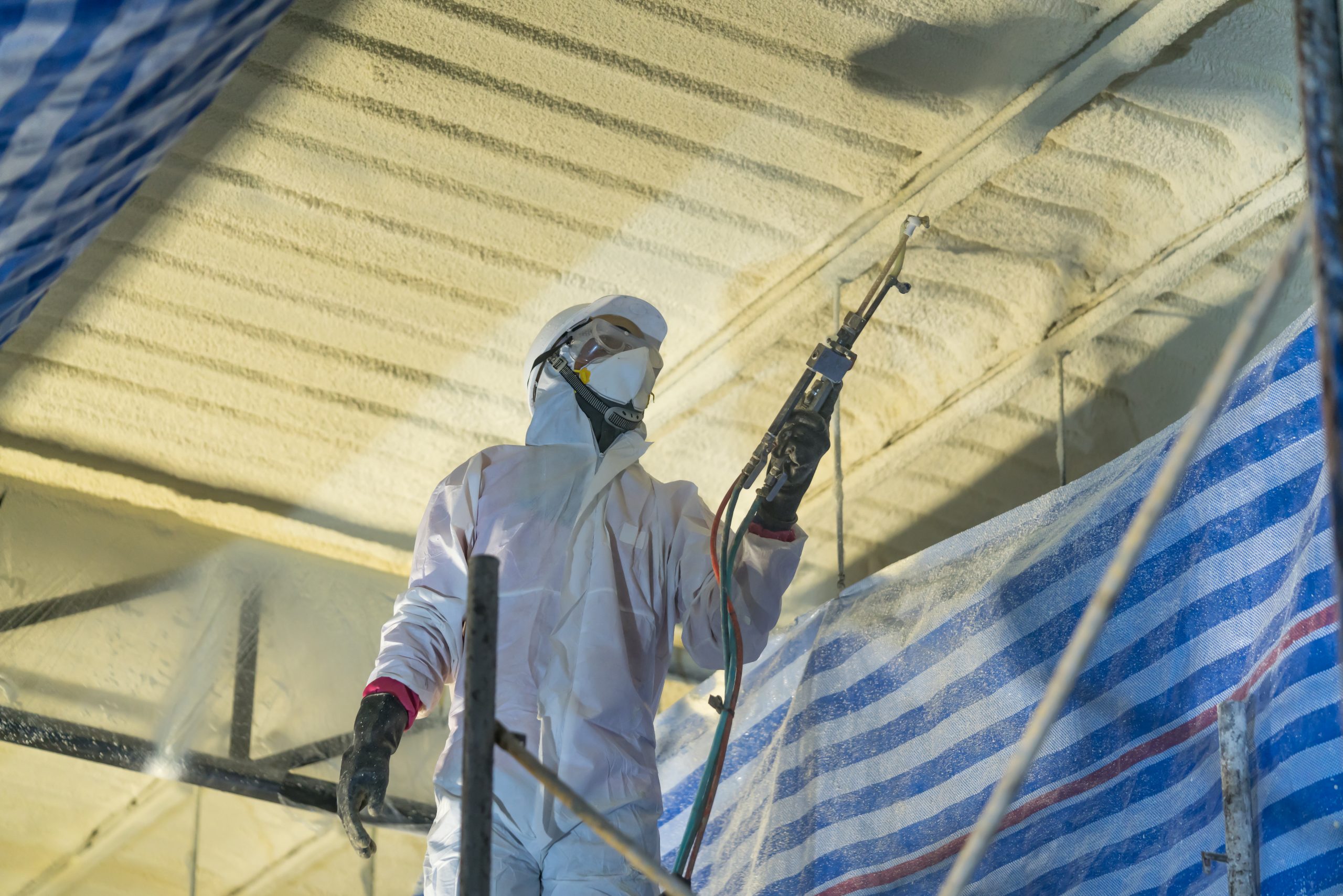
What To Consider When Using a Spray Foam Roof
As one of the most versatile plastic materials, polyurethanes are everywhere. Polyurethanes can solve all sorts of challenges. Like how to put a roof on your commercial building that’s durable, flexible, lightweight, renewable, waterproof, and easy to install and maintain. Here are some spray foam roofing basics that’ll help you make the right solution.
The solution you’re looking for is spray foam roofing. When it comes to energy efficiency and long-term performance, spray foam roofing is tough to beat.
Spray Foam Roofing Explained
Spray polyurethane foam (SPF) is a plural-component chemical product created by blending two materials, isocyanate and polyol resin. These two elements react when mixed together under heat and pressure. This significantly expands the liquid volume. When used for roofing purposes, once the substance hardens, a solid, fully adhered roofing membrane results. Commercial structures are a great candidate for SPF roofing. It efficiently covers large surfaces and does not add significant weight.
There are several layers to your spray foam roof.
First
An existing roof or decking forms the base. This underlying layer or substrate supports the foam system. Any number of materials can make up this layer. Including whatever built-up roofing, modified bitumen, EPDM, PVC, TPO, metal, or concrete is already in place. (Some may require the installation of a cover board prior to the application of foam.) Clean the base thoroughly to remove dirt, dust, debris, and other contaminants. This is to ensure maximum adhesion.
Second
The next step is applying the substrate with polyurethane foam spray. It is necessary to use a specialized spray foam rig. A separate container houses each chemical that makes up SPF onsite. Then pumped through high-pressure hoses to a mixing gun at a temperature between 115-130° F. After application, the SPF liquid expands and solidifies into a dense foam membrane. It is typically 1 to 1.5 inches thick, as it cures. The polyol component determines the thickness of the foam. Needing a density of 2.7-3.0 lbs. The foam is rigid enough to walk on without causing damage. This is important for commercial purposes.
Third
An elastomeric coating of silicone, acrylic, urethane, or butyl rubber protects the foam from UV exposure and other elements. It may need two layers. This depends on climate, location, warranty, and other requirements. The top layer is often reflective to increase energy efficiency and shield against UV rays.
Final
Finally, #11-grade roofing granules are broadcast into the elastomeric top coat. These bits of crushed stone add strength, durability, UV protection, and resistance to wildlife to the foam membrane that covers up the roof.
Understanding that installation of SPF roofing system is not a job for amateurs is essential. One must have significant knowledge of SPF chemistry. The equipment requires an expert. Technicians must be properly trained on all aspects of SPF technology. They have a proficiency that can take years to acquire. To make sure you’re working with a certified SPF contractor, ask to see job references, industry certifications, case studies, product samples. If possible, arrange an in-person roof walk of a recently completed project. Any qualified contractor is proud to show off the company’s work.
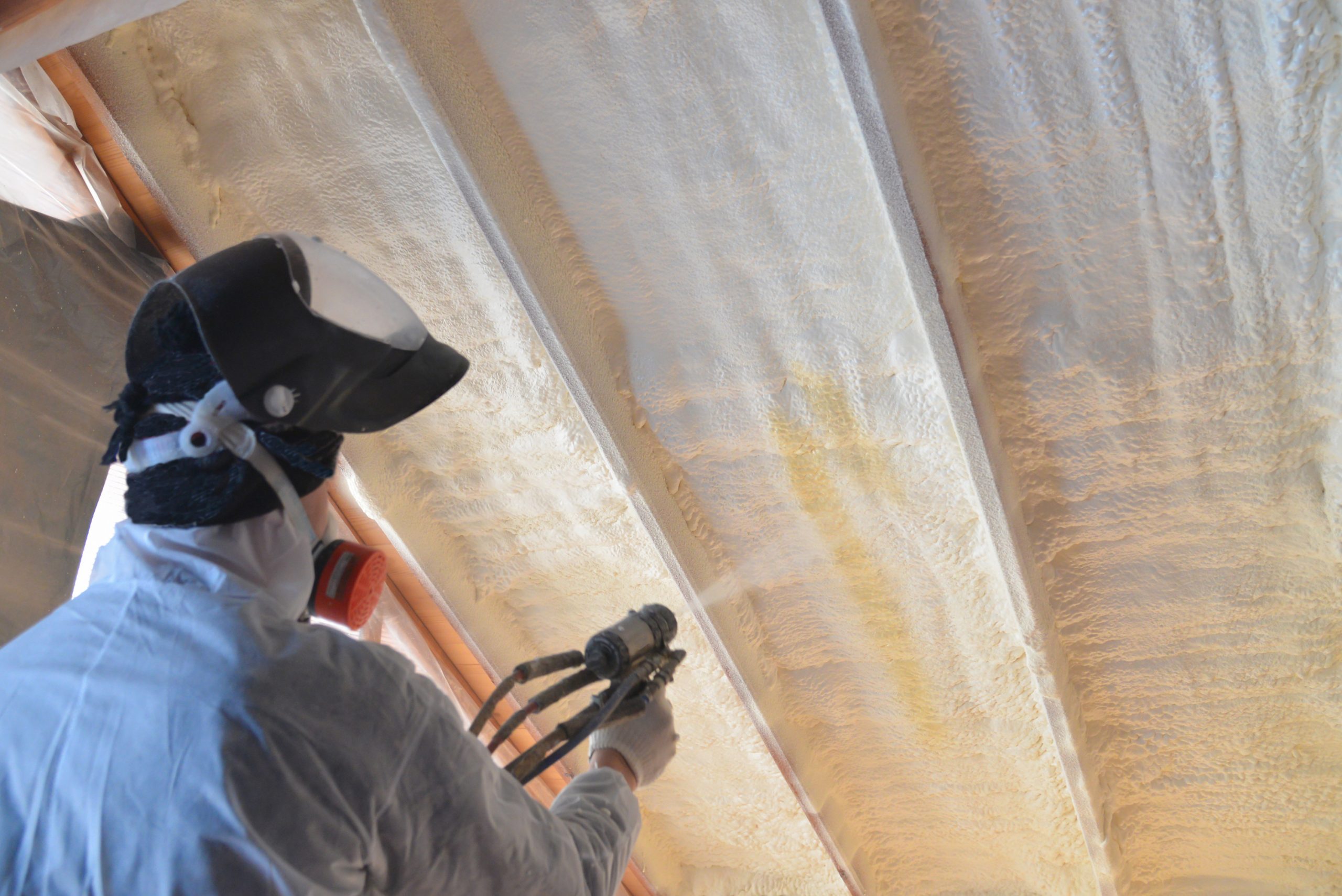
The Pros of SPF
For facility managers and property owners alike, the benefits of SPF are impressive.
That starts with thermal resistance: Spray foam has the highest R-value of any conventional roofing material. R-value measures a material’s capacity to resist heat flow. Keeping your building cool is easier with SPF’s R-value of 6.6 per inch of thickness. These insulation properties translate into lower energy bills, which is especially important given the relentless escalation of costs. The longevity of SPF roofing—a properly installed and maintained system will last a minimum of 20 years and often 30 or more—delivers significant savings over the long haul.
In Comparison
The installation of SPF is faster and less disruptive than that of other commercial systems. . Among the reasons: No tear-off of existing roofing saves time and mess. There’s less odor than with other types of installations, especially built-up tar and gravel. The self-contained nature of SPF means fewer materials need to be hauled to the rooftop, and the risk of objects blowing or falling from the roof is reduced. Being able to spray around penetrations for HVAC, pipes, curbs, and skylights is a real advantage. Within 30 seconds of contact, foam conforms around such irregularities and grows to close cracks and seal crevasses. Contrast that with other systems and the hours consumed by manually fitting flashings, installing fasteners, and taping gaps.
And since SPF roofs are seamless, waterproofing is enhanced. Foam is sprayed in one continuous layer, without nooks, crannies, and overlaps for water to seep through. The closed-cell nature of the foam (ask your contractor to explain the chemistry) resists standing water and absorption as well. Should damage occur, generally it can be repaired with roofing-grade mastic or sealant.
Understanding SPF Downsides
Of course, nothing is perfect, including SPF.
For best results and maximum longevity, care and attention to the membrane are required. Twice-yearly inspections by a qualified roofing contractor trained to spot issues from debris, weather, wildlife, foot traffic, ultraviolet radiation, and other impacts are recommended. Every decade or so the elastomeric coating must be reapplied to protect the foam below.
Potential health hazards from fumes during installation and curing are of concern, and these can linger if a building if not properly ventilated. For workers doing installation or maintenance, wearing protective equipment is a must. Overspray during application is another concern; structures, property, vehicles, and people near your building must be moved or protected from droplets that stray from the roof onto objects below.
Understanding the limited application window is essential. SPF will not stick when moisture, frost, or ice are present, and the foam fails to form correctly if temperatures are too low. The system must be installed on days above 50° F, in relatively low humidity and calm wind. Depending on geographic location and season of the year, SPF application may have to wait for favorable conditions, so careful planning and a degree of flexibility are required.
The SPF Bottom Line
Although SPF has a reputation for being somewhat more expensive than other roofing systems, working with a qualified professional is the only way to get an accurate reading on actual price. Your contractor partner can help you analyze the many factors involved in your decision—the size of your building(s), age, purpose, location, climate, people, equipment, surroundings, and how best to protect the structure and what’s happening inside. Given the ease of installation, durability and insulating qualities of materials, and long-term energy efficiency, spray foam may be your ideal commercial roofing choice.